ArcelorMittal is the global market leader in the steel and mining industry. Part of this leadership is thanks to the job of its Global Research and Development (R&D) department, constantly supporting all the segments throughout the company business. We are permanently searching for the excellence and looking for technological advances that allow us to make new steels while improving manufacturing processes. This commitment to innovation extends beyond new products and processes to encompass how we can, positively, impact the life of people all over the world.
Nowadays, ArcelorMittal Global R&D team employs around 1,500 full-time researchers at 12 sites throughout the world, with centres strategically located in Europe, North and South America and close to key operations and customers. These centres are where new steel products, processes and solutions are envisioned, tested, improved and deployed.
ArcelorMittal’s investment in R&D activities, keeps us at the forefront of innovation and ahead of competition as steel manufacturer of choice for our customers.
ArcelorMittal Rails & Special Sections bringing innovation to the railway sector
The need for fast and reliable transport has stimulated R&D in this sector, making it possible to overcome challenges unimaginable a few years ago. ArcelorMittal, in its continuous development, has reinforced this permanent evolution in the rail sector with improvements in product range and bringing new rail products with tailored properties.
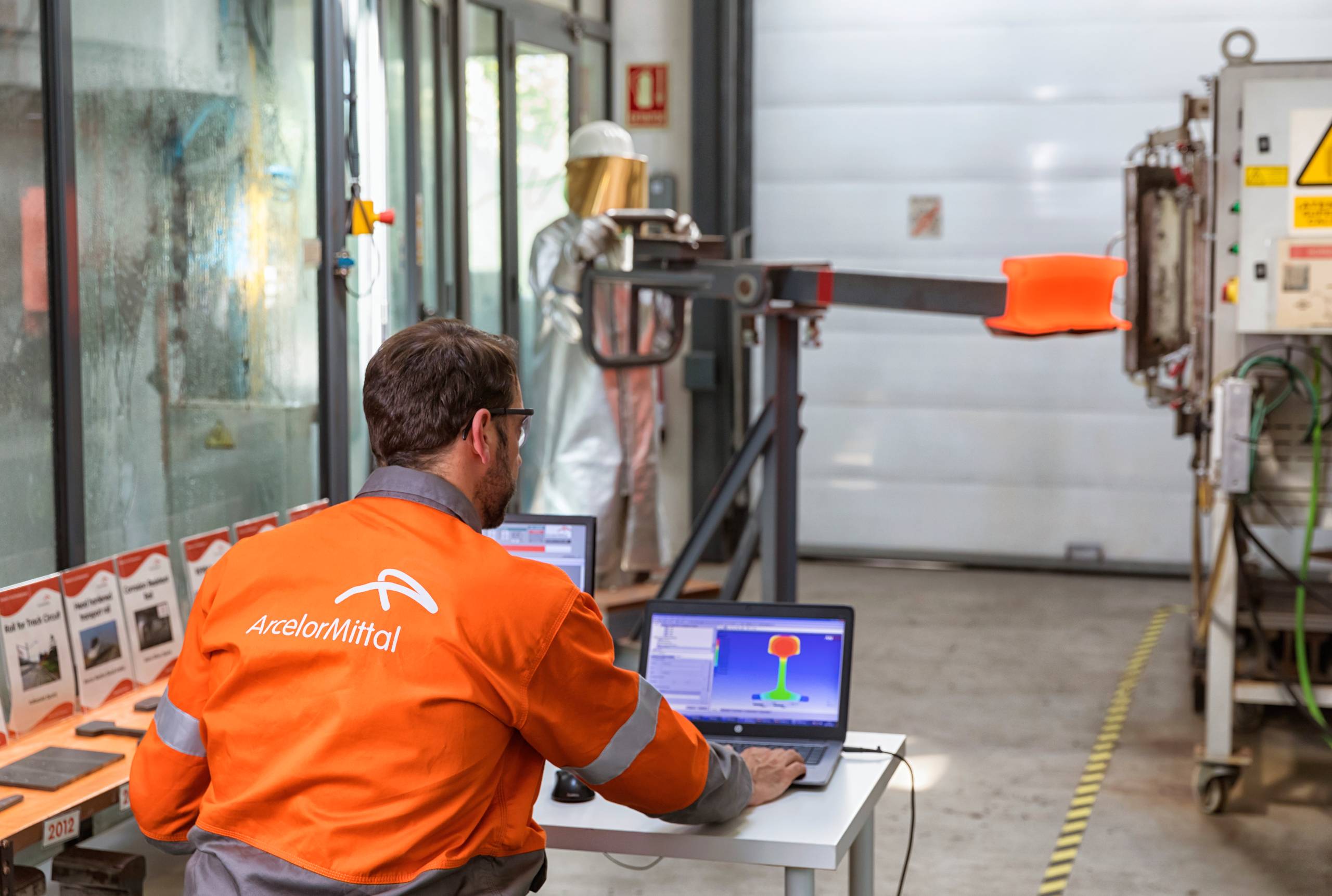
Established more than a decade ago, ArcelorMittal has its own dedicated R&D Rail Excellence Center, located in Northern Spain, to provide our customers with prompt, innovative and cost-effective solutions. The research lines are structured around three main axes: optimization and digitalization of the rail manufacturing process, new product development for all the segments within the railway market and the implementation of new rail-based track solutions.
All these developments are strongly supported by unique ArcelorMittal facilities that reproduce, in its laboratories at industrial scale, the full product development cycle starting from laboratory casting stage, passing through the hot rolling, carrying out additional thermal treatments as the rail head hardening, and getting to test final properties as the weldability or the validation of in-use properties, for instance its rolling and corrosion performance. Developments are further strengthened with an open innovation philosophy in collaboration with a network of top universities, leading technology centres and the main companies from railway sector that are materialized in unique equipment built around the Steel Block facilities.
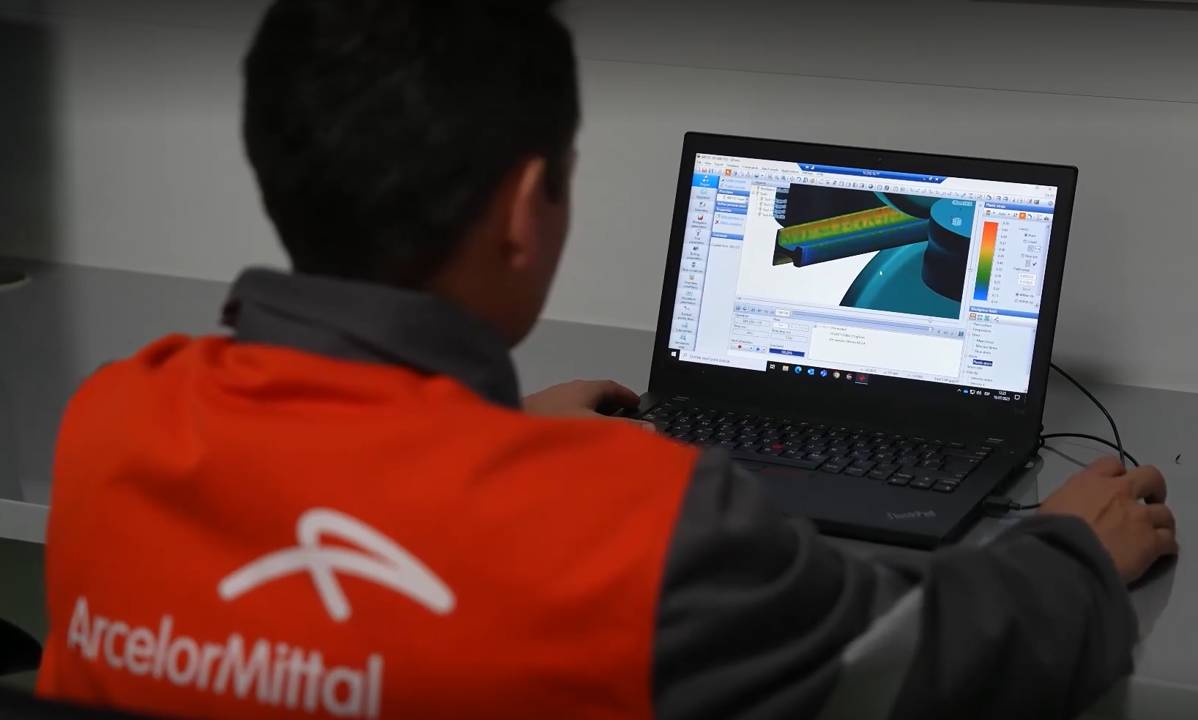
Some examples of ArcelorMittal’s current main trending topics for railway are the increase in rail length in order to provide further track safety, welding, track laying and maintenance cost savings, and the increase of rail service life with the most appropriate solutions related to different applications such as low carbon grades for tramway, new hardness grades for heavy haul and other uses such as cranes.
Recent R&D contributions
Willing to expand ArcelorMittal rail catalogue, R&D has recently contributed to the development of some remarkable products and solutions. Among them, some examples of technological advances, aiming to help our customers in the solving of some their on-track issues:
- R340 Crane: This new product combines optimum process parameter with ad-hoc chemical composition. In-service performance show that R340 is benchmark in wear resistance compared with other crane rail grades available in the market thanks to its customized microstructure.
- R290V: ArcelorMittal R&D team has worked on the development of a complete range of Low Carbon Vanadium (LCV) grades for grooved rails which provide better performance and increased service life for Light Rail Transit operators. The addition of vanadium allows to enhance in-use properties, like its wear resistance or fatigue behaviour, always ensuring the proper steel grade weldability.
- RailCor®: This solution allows to increase the lifespan of those rails installed at extremely corrosive environments. RailCor® product family is a completely new range of corrosion-resistant rails which offer protection in severe environments in terms of corrosion. Apart from the corrosion protection itself, these products count with additional enhanced functionalities, like the mitigation of stray currents effects. Products are designed to be installed inside tunnels, city centres, or coastal areas. RailCor® offers increased rail service life and expense savings reducing Life Cycle Cost.
- Life Cycle Cost (LCC) models for transport rails: Based on sustainability approach and cost saving principles, ArcelorMittal Global R&D has implemented LCC models with the objective of offering customers the very best steel grade for their specific track characteristics. This digital platform allows end-customers to select the best option, both technically and economically, to solve their maintenance and on-track bottlenecks.
These are some of the most recent examples, but for sure that will not be the last ones. Breakthrough topics are also covered within our R&D portfolio and will see the light in the very close future.
Please keep updated for the new developments to come!!
More information?
If you wish to learn more about our services or you have any questions, please contact us.